BOOK 3: The ProDUCT
8th APRIL till 27th July (Today): THE LONG ARDUOUS MARCH
As this tale is being written up today, 110 days since D1 and D2 were born within 2 to 10 days of conception, a product has not yet been released by the team. D2 has been all wrapped up in a nice package and even more importantly has completed 120 hours of continuous working without failure. The team is looking at that data. The process of converting D2-the prototype to D2-a reliable product threw up flaws that the team hopes to address in D3. Then 3 prototypes will be made and will undergo certification. Then there will be animal tests and short term human tests before either D2 or D3 can be released as a full fledged ventilator.
The team could have released D2 as it meets the requirements set out in the beginning of the COVID situation for emergency ventilators. However, given the current scenario, in which it is being suggested that high oxygen flows through a nasal canula are the first round of therapy, followed by CPAP, the team has decided to ensure that the ventilator it puts out is well certified and is a properly tested instrument.
How would these be different from existing ventilators. It would be a lower cost solution. The control code developed at IISc, that is going to go in free of cost, would be the primary enabler. The long hours spent on it by Saurabh, Sushobhan, Harsha and the others who developed it are priceless.
The team could have released D2 as it meets the requirements set out in the beginning of the COVID situation for emergency ventilators. However, given the current scenario, in which it is being suggested that high oxygen flows through a nasal canula are the first round of therapy, followed by CPAP, the team has decided to ensure that the ventilator it puts out is well certified and is a properly tested instrument.
How would these be different from existing ventilators. It would be a lower cost solution. The control code developed at IISc, that is going to go in free of cost, would be the primary enabler. The long hours spent on it by Saurabh, Sushobhan, Harsha and the others who developed it are priceless.
Here is a photo story of the “Arduous March”:
April 5: Prosenjit makes the GUI.
He, Sushobhan and Saurabh get the Raspberry Pi, the “display unit” on which the GUI will run talking to the Arduino on which the control runs.
April 5: Prosenjit makes the GUI.
He, Sushobhan and Saurabh get the Raspberry Pi, the “display unit” on which the GUI will run talking to the Arduino on which the control runs.
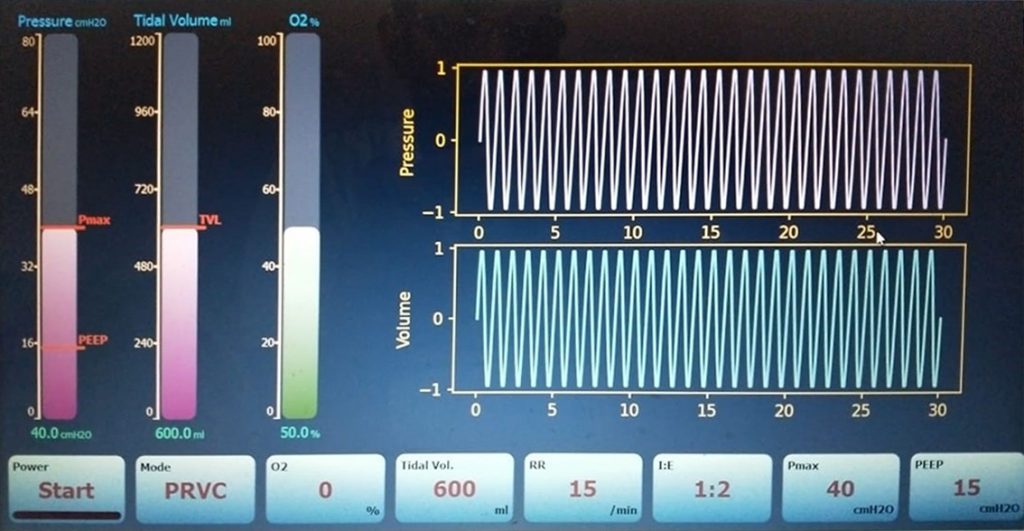
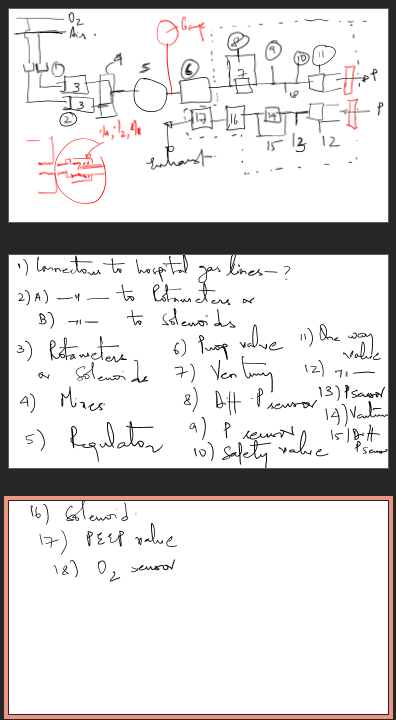
April 18th (18 days later): The ENTIRE inspiration and expiration blocks will be monolithic 3D printed blocks. Having tasted the advantages of 3D printing in enabling flow control the team decides that the entire inspiration and expiration block, essentially all the pneumatics of the ventilator will be a monolithic 3D printed block. Harsha, Ankit and Vasu start working on these blocks and their design requirements. Over the next two months this block will undergo multiple design iterations and manufacturing overnight (literally) all of which would not have been possible with the technological development of the 3D printer. (Authors note: The routine would be a design discussion in the morning.
Followed by a CAD design by the evening and a print command at night. Each block would take about 24 hours to print. Thanks to RP for graciously throwing open the doors of his lab to allow us to use his 3D printer). This compact 3D printed blocks are also the reason why the ventilator itself is so compact.
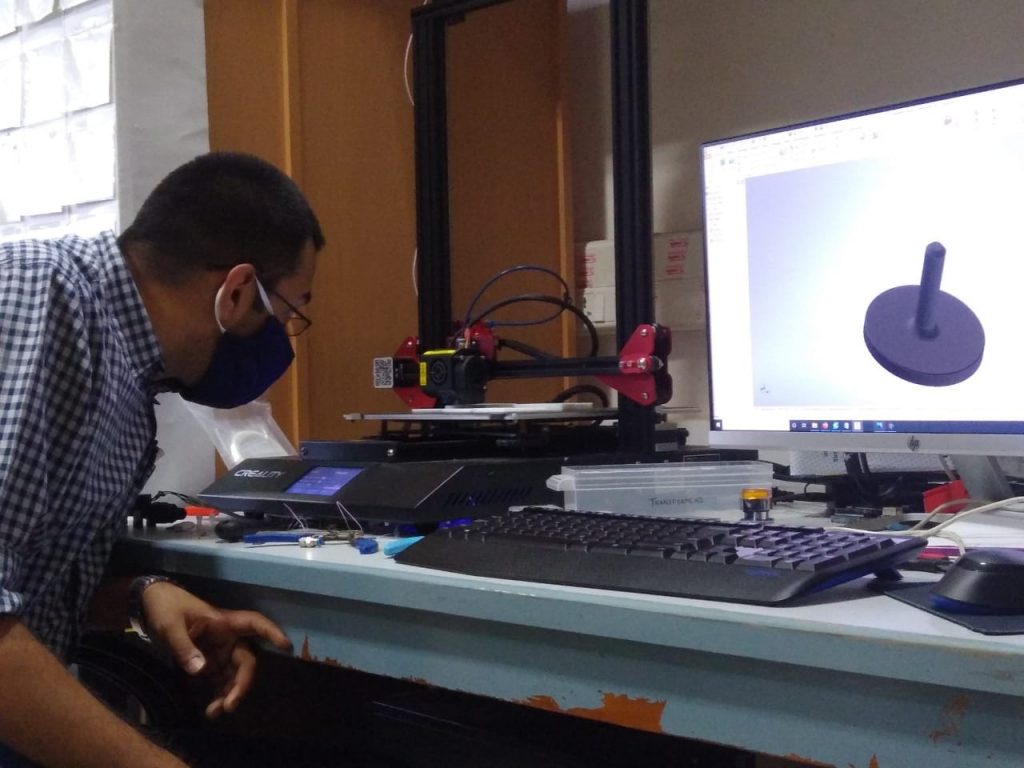
April 22 (15 days later), The Board Arrives: The electronic board coordinated by Sushobhan, G. Narayanan, Harsha and Kapil arrives. Even though the first cut design was ready, it was not easy to source all of these components, make the PCB and then populate it with the components. A big source of current delay is the control electronics for D3 that tackles issues in the first board.
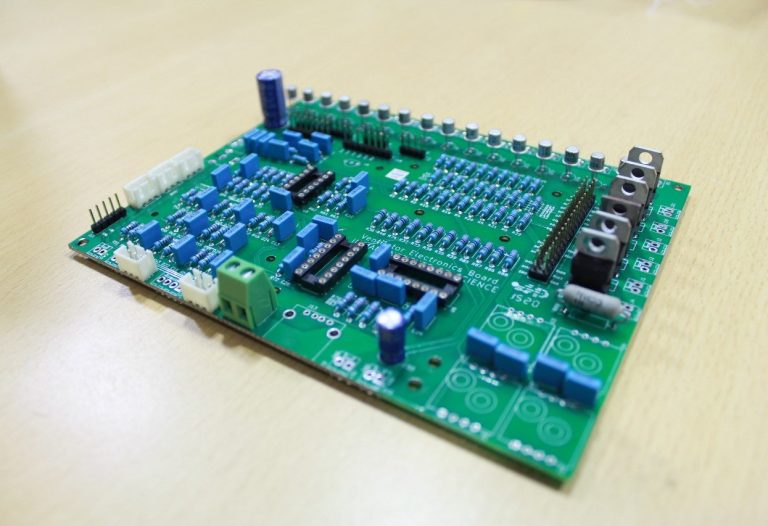
April 28 (21 days later): The first design and VASMED. (Author’s note: Around the time the team had completed D2 in early April and had started thinking about testing and certification, Vasu got in touch with VASMED, a bio-med company that he had interacted with, for help with compliance. Anoop Varghese, the MD of Bengaluru operations, readily agreed and since early April to now Anoop was an integral part of team meetings quietly providing suggestions on what is required for Bio-Med equipment. He and Akshay Naik had being laying the ground work to get the testing done, while the rest of the team was getting the ventilator built.) As of today, the 29th of July, the team is populating the excel spread sheets that they had developed during these months. Based on past experience, Vasmed comes up with a quick and simple design for the sheet metal exo-skeleton, that would eventually envelop the first D2 prototype.
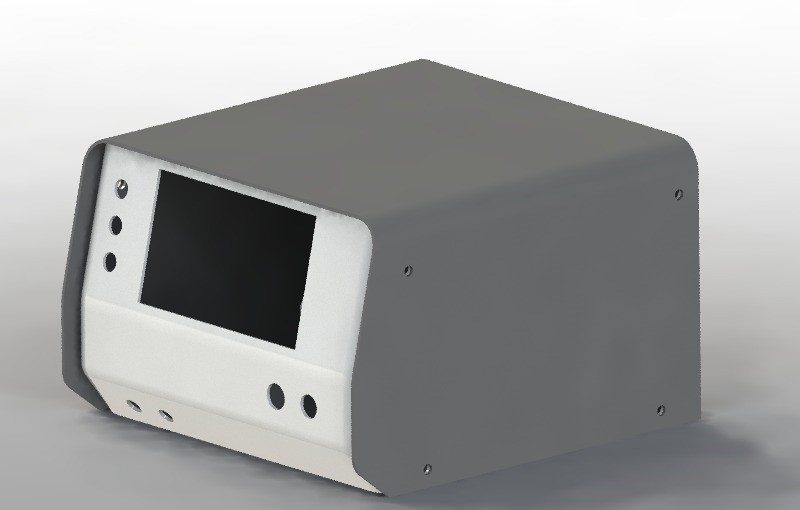
May 7th (30 days later): A very critical component an external calibration source becomes available: While the team has more or less put together its ventilator, it was desperately searching for an external unit for calibration purposes. There are many such units in the country but the lockdown makes it impossible to access them. At last on the 7th of May VASMED helps get a unit with calibrated pressure and flow sensors. The team then tests its ventilator on his system and for the first time is convinced that it has a working machine.
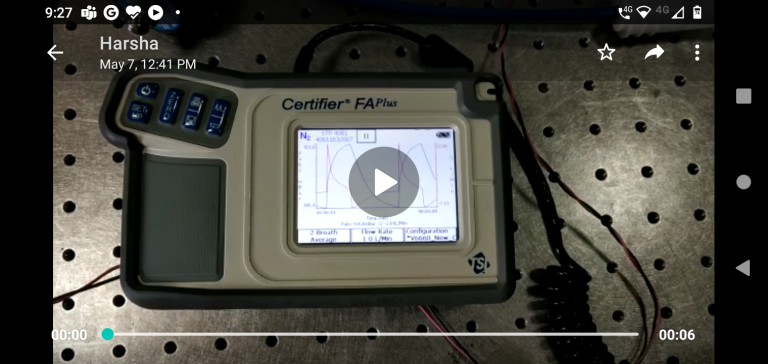
May 8th (31 days later): The “Dabba” arrives: The team at CeNSE is used to calling the external package a dabba. It’s a term coined out of frustration. One may make the best product in the world, but unless it is packaged properly it will not sell. Through the lockdown VASMED gets in touch with a sheet metal fabricator in Peenya and gets the first dabba to CeNSE. Its one thing to make a prototype and another to populate components inside the all important sheet metal enclosure. Harsha and Ankit start working on it. “Oh! no!. This board is bigger by 1 mm or that hole is smaller by 0.5 mm” are common frustrations. This is part of every prototype development no matter the degree of design and digitization. Unnikrishnan, the VASMED design engineer, works with files and saws and helps put D2 together. It will take 10 more days for all the component sizes, fittings and connections (pneumatic and electrical) to fall in place within the exoskeleton.
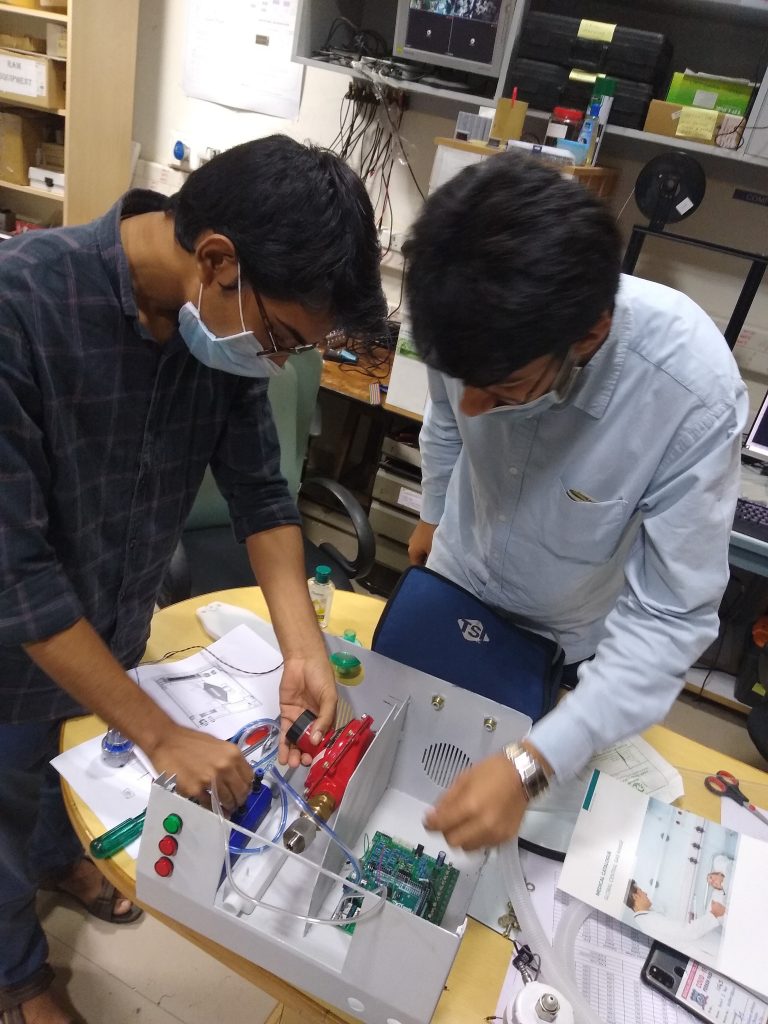
May 18 (41 days later): The first prototype testing starts:
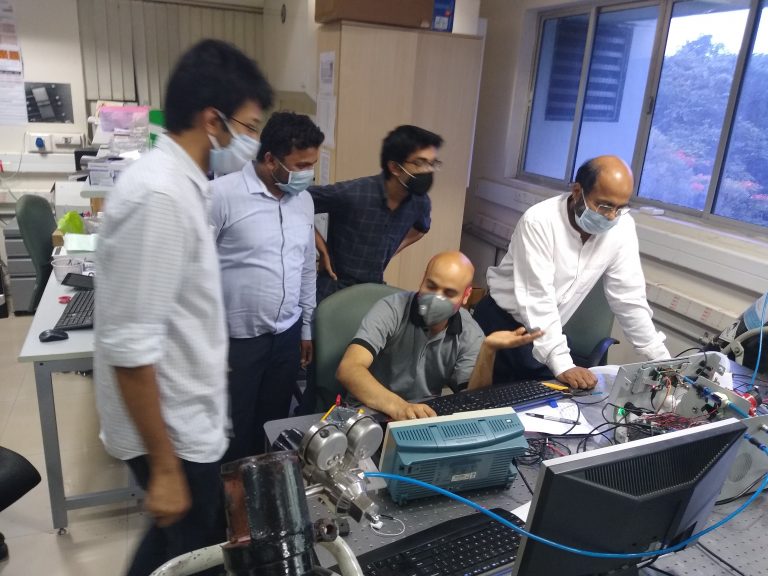
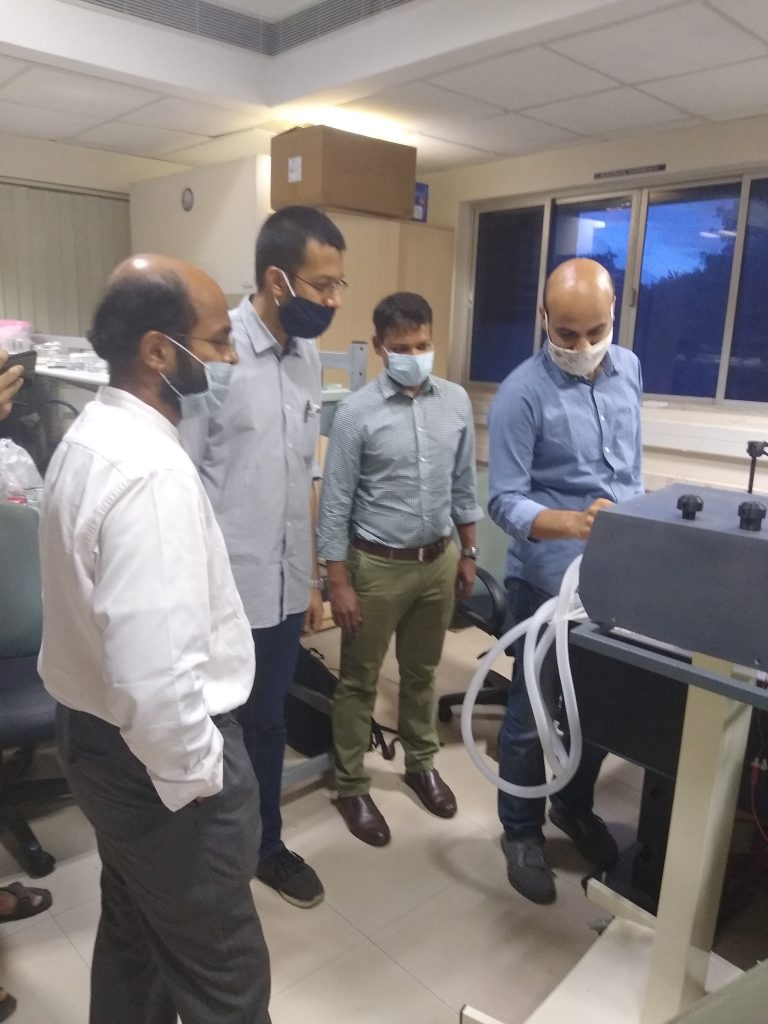
June 4 (58 days later): The Team is confident enough to show it to the Doctor. D2 is now on a trolley (thanks again due to VASMED) and all packaged. It still needs to be tested on lungs with various resistances and compliances. Such a lung is not available in India and it will not be till the middle of July when VASMED imports such a lung from the US and provides it to the team.
Vasu, the coordinator is not very happy with the demonstration. The next day at a team meeting he is blunt and states that this will not sell. For a product he expects everything to run smoothly. The team is upset. They get back to the drawing board and pencil out the rough edges. A critical factor that emerges is that a control specialist is required. Prof. Jayanth from Instrumentation in IISc is pinged and he agrees to pitch in. (Author’s note: Discussions, differences and deviations from the original plan are part of any such development. A good team is one that knows that they can be brutally frank and blunt internally…all to achieve the common agreed upon team goal)
Vasu, the coordinator is not very happy with the demonstration. The next day at a team meeting he is blunt and states that this will not sell. For a product he expects everything to run smoothly. The team is upset. They get back to the drawing board and pencil out the rough edges. A critical factor that emerges is that a control specialist is required. Prof. Jayanth from Instrumentation in IISc is pinged and he agrees to pitch in. (Author’s note: Discussions, differences and deviations from the original plan are part of any such development. A good team is one that knows that they can be brutally frank and blunt internally…all to achieve the common agreed upon team goal)
June 15th (69 days later): The product, D2, is ready to be unveiled. D3 is still getting made.

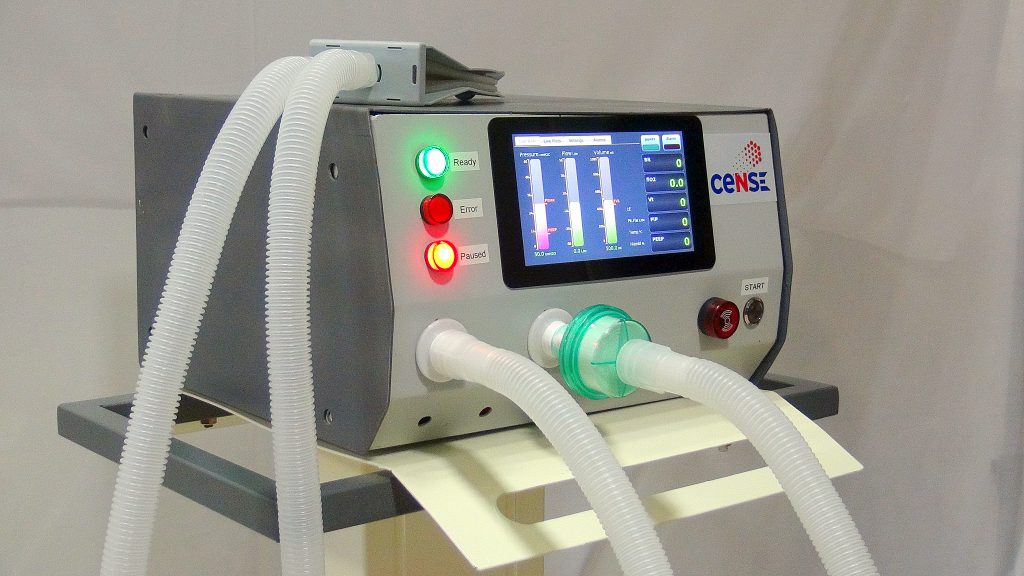
June 26-31st (85 days later): 120 hours of reliability testing is completed!
29th July final Note: In the next 14 days the team hopes to assemble D3. Post testing, it will go for certification. It is hoped that it will be completed in August. The product will then be shared with companies that we are confident will do a reliable manufacturing job. The team needs to ensure that this goodwill gesture in these times will not bring liability upon IISc in any form and are preparing the groundwork for the same. Please look up our website for all contributors to this project.
29th July final Note: In the next 14 days the team hopes to assemble D3. Post testing, it will go for certification. It is hoped that it will be completed in August. The product will then be shared with companies that we are confident will do a reliable manufacturing job. The team needs to ensure that this goodwill gesture in these times will not bring liability upon IISc in any form and are preparing the groundwork for the same. Please look up our website for all contributors to this project.